explorative product design research
Custom Synthesizer casing
Project Type
Client
self-initiated
Year
2013
This project has been an exercise, primarily, to learn more about laser cutting techniques in wood and, secondly, to investigate how the inherent aesthetics of lasercut wood could be used to add more character to a product. As a test case I have designed a new enclosure for a musical instrument that I felt needed some more character.
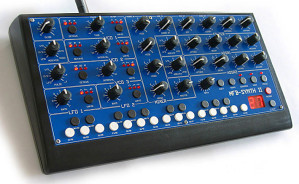
The original MFB Synth II in its (purchased part) ABS enclosure: functional, but missing some character.
(Photo by Patrik Lark)
The new casing is presented below, if you would first like to know what was the underlying reason to embark on this investigation, then it's best to start at the bottom: why?
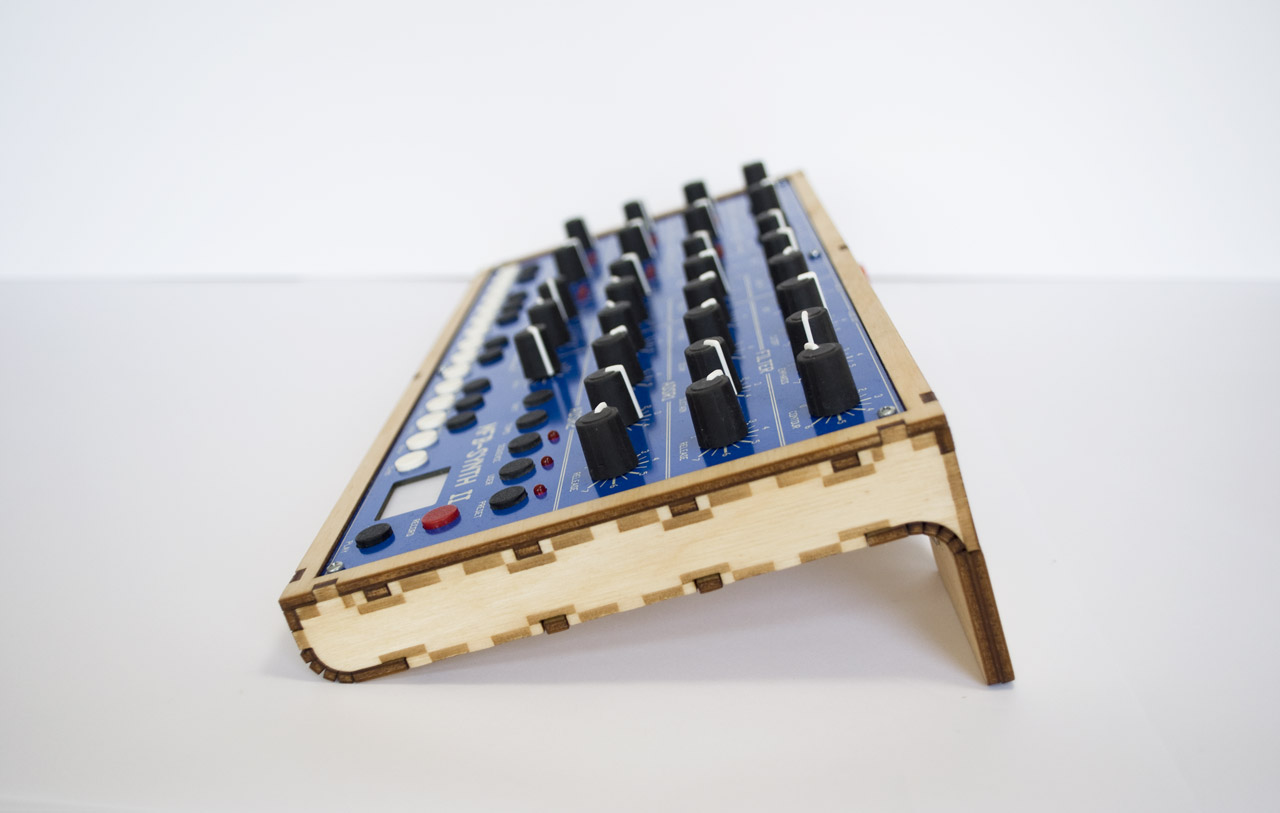
The new laser-cut casing.
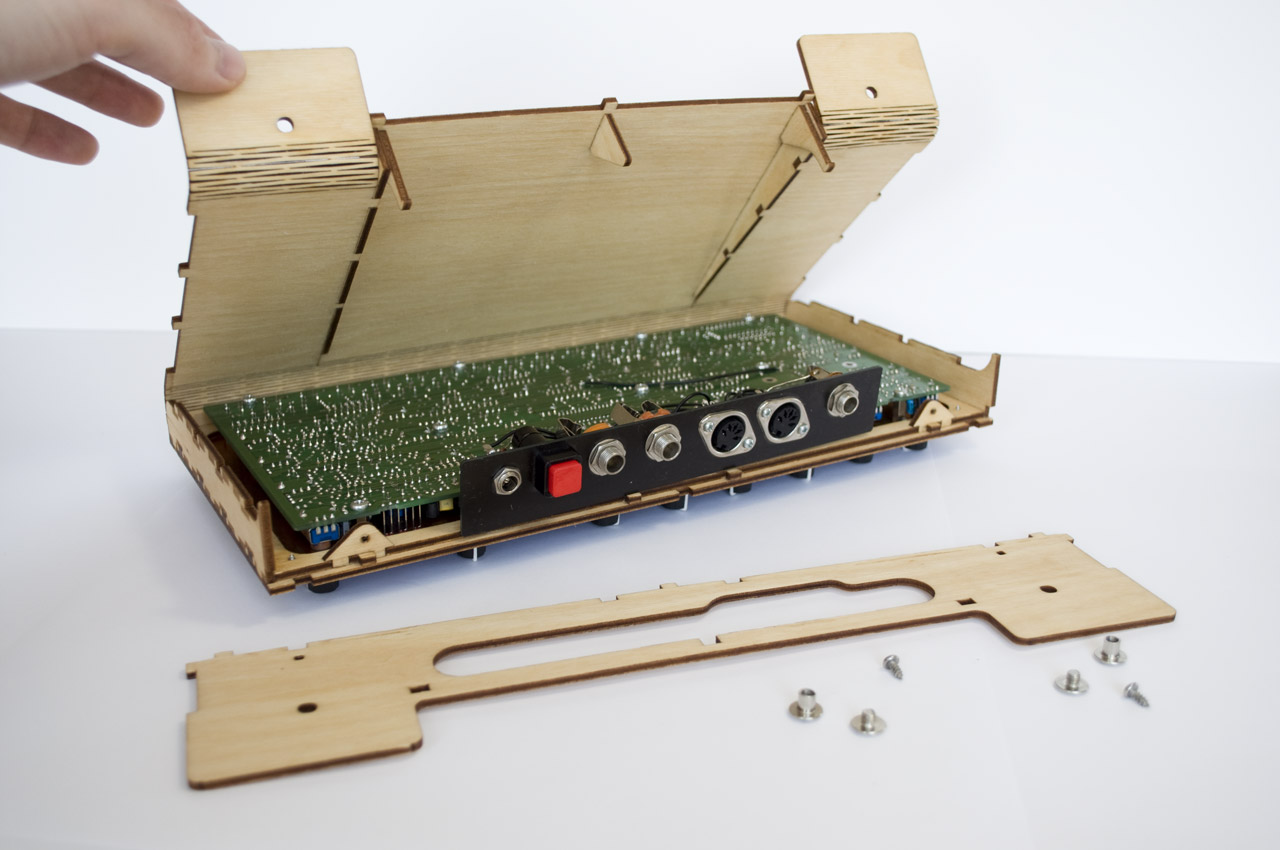
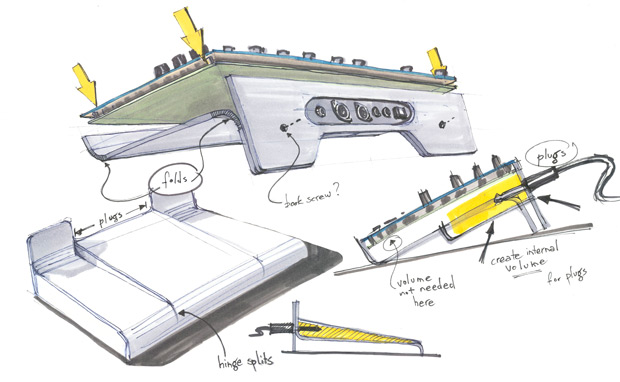
Development
Construction

For laser cut enclosures there lies a task in finding an efficient way to form a closed box with few connections and a minimized spatial footprint. The flat board is the basic material and to shape it into an enclosure with as few components as possible I applied a folding technique (with a perforation pattern) that has been popularised by the guys at Snijlab. This way the front, bottom and the feet of the ‘box’ could be made out of one component.
Apart from the rear panel, which can be opened for maintenance/servicing, the panels of the enclosure are glued together. With the tight fit of the laser cut wood this makes for an indestructable connection. The back panel is mounted with four screws. The top-panel of the enclosure is built out of two layers to optimize the rigidity of the enclosure and to enable a smooth edge around the control panel.
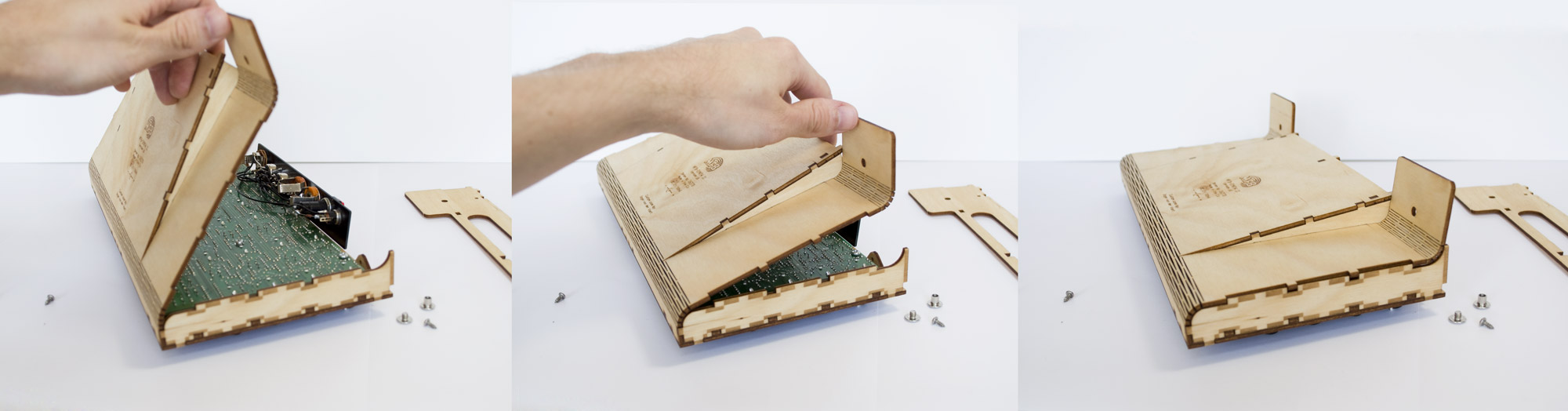
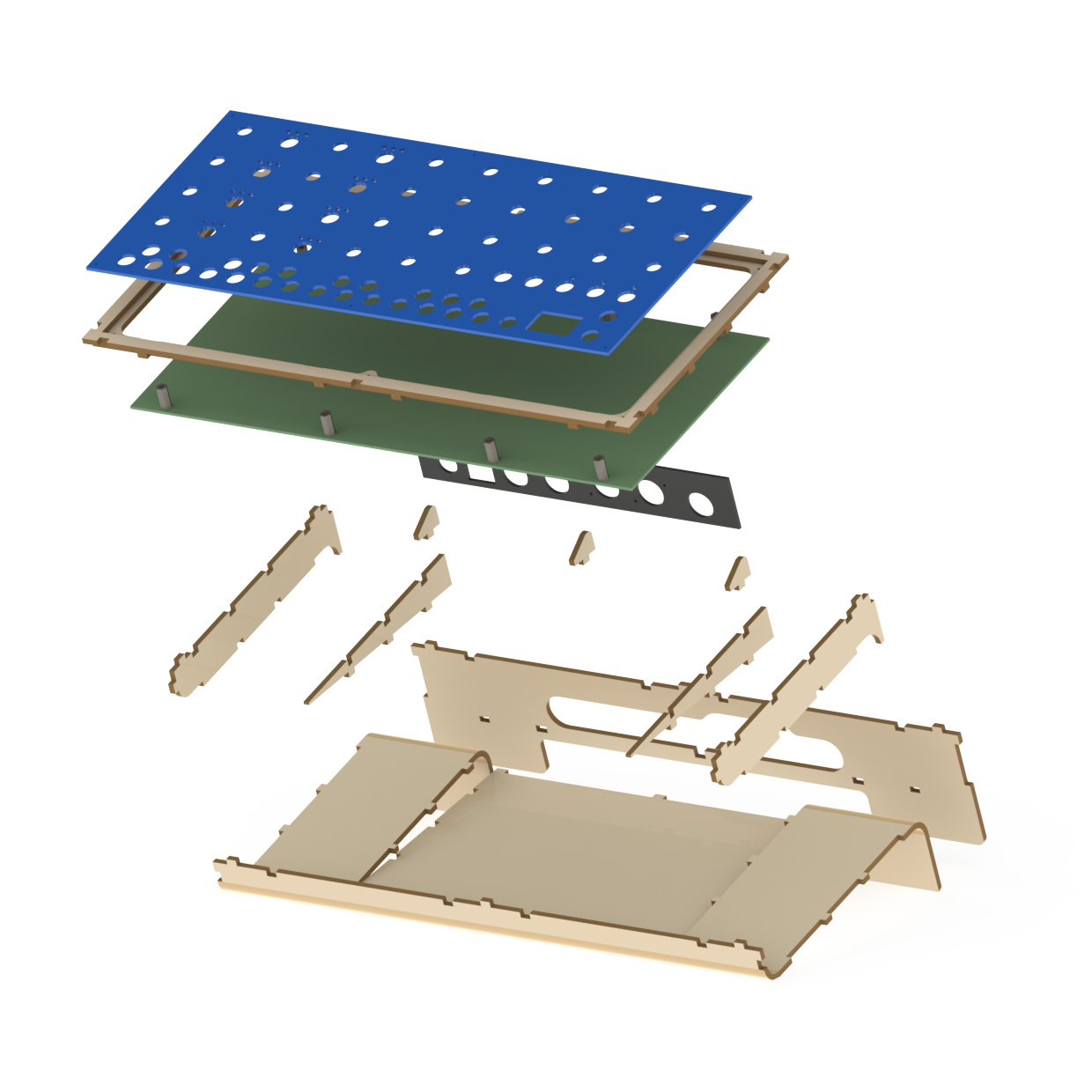
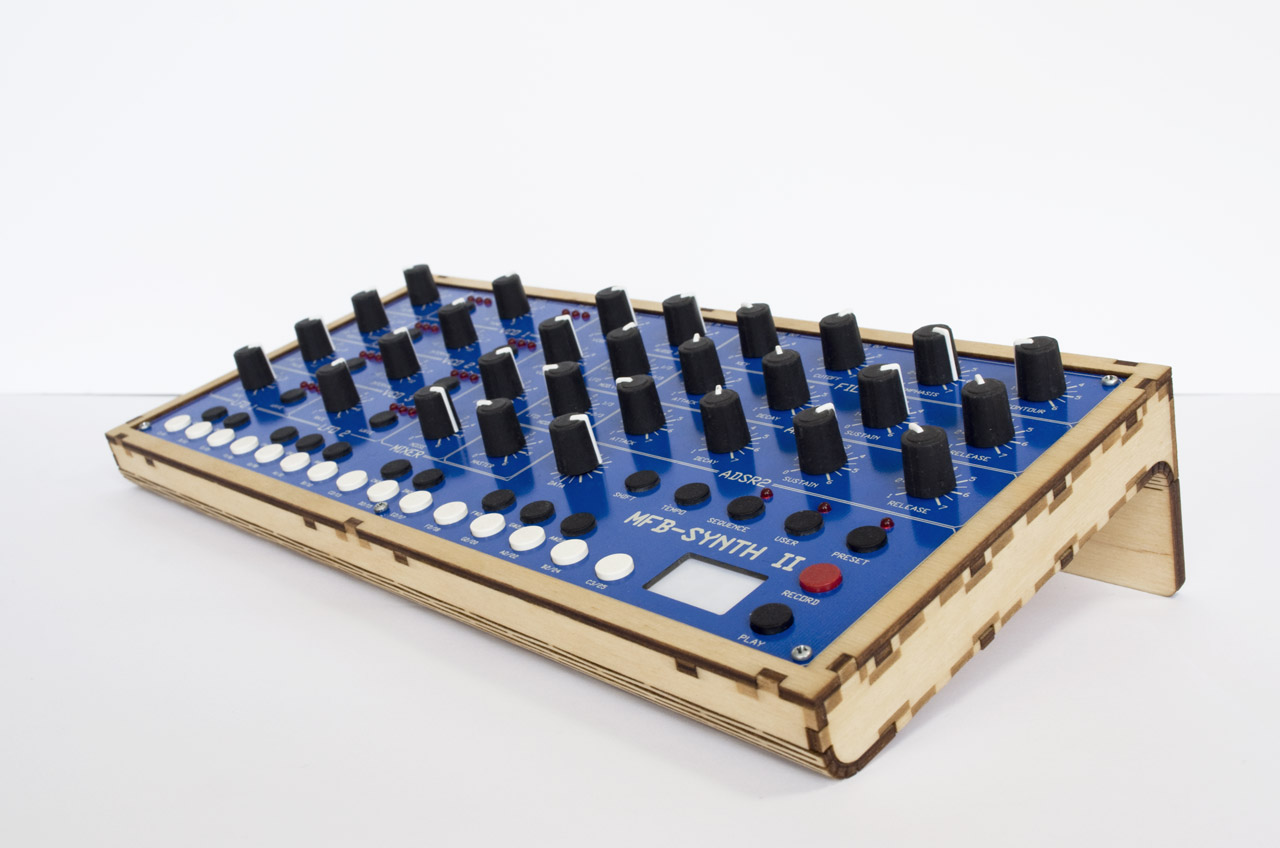
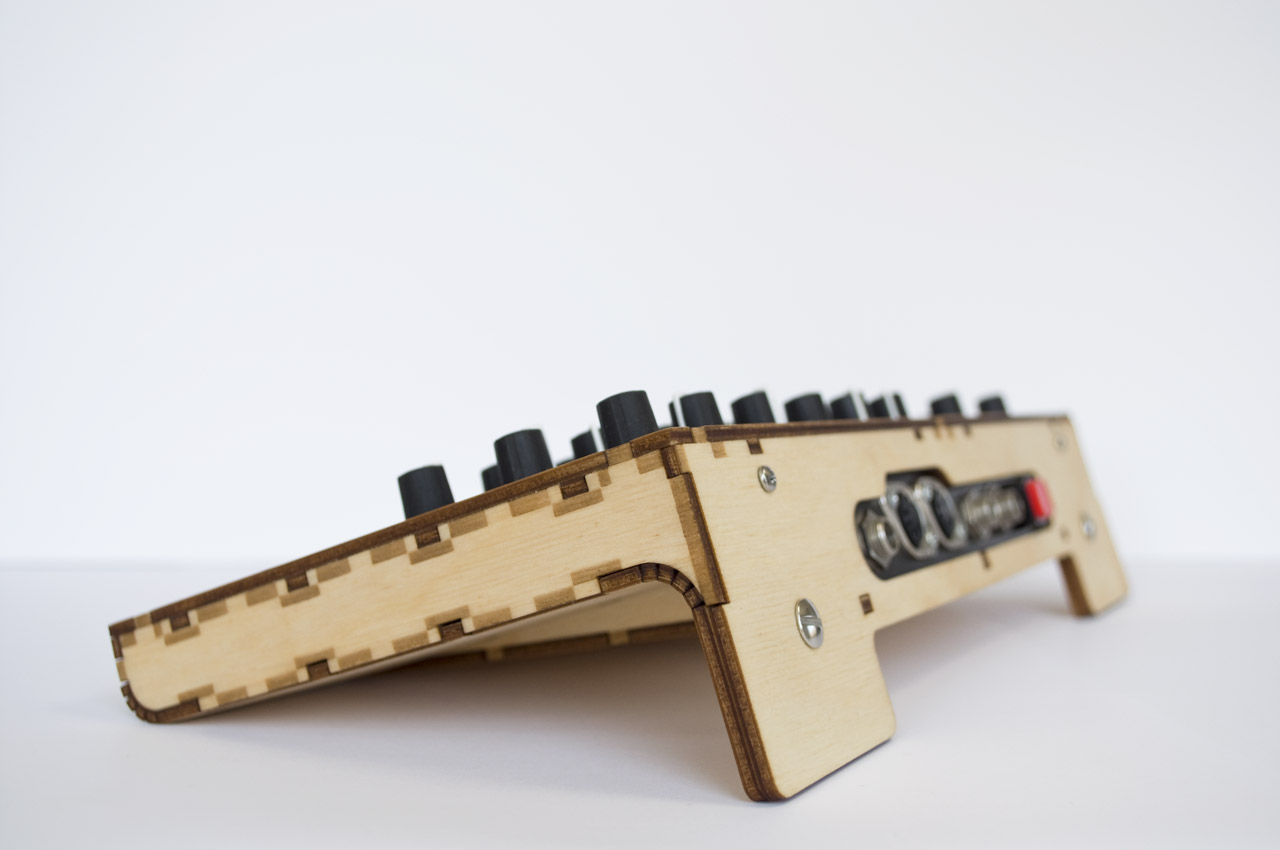
Aesthetics
Handmade quality in an electronic instrument

When you lasercut wood, you will always end up with burnt sides of the board. Because of the visual effect that these burnt edges have on the appearance I looked for a way to incorporate these edges in the design, all to avoid the ‘toy box’ appearance that many laser cut enclosures have.
Following the theory ‘if you can’t hide it, emphasize it’, I have combined the darkened edges of the board with laser pattern engravings, to obtain a similar effect as in the wooden inlays on spanish guitars. Together with the engraved block shapes the corner joints form a pattern, similar to these inlays or embroidery patterns.
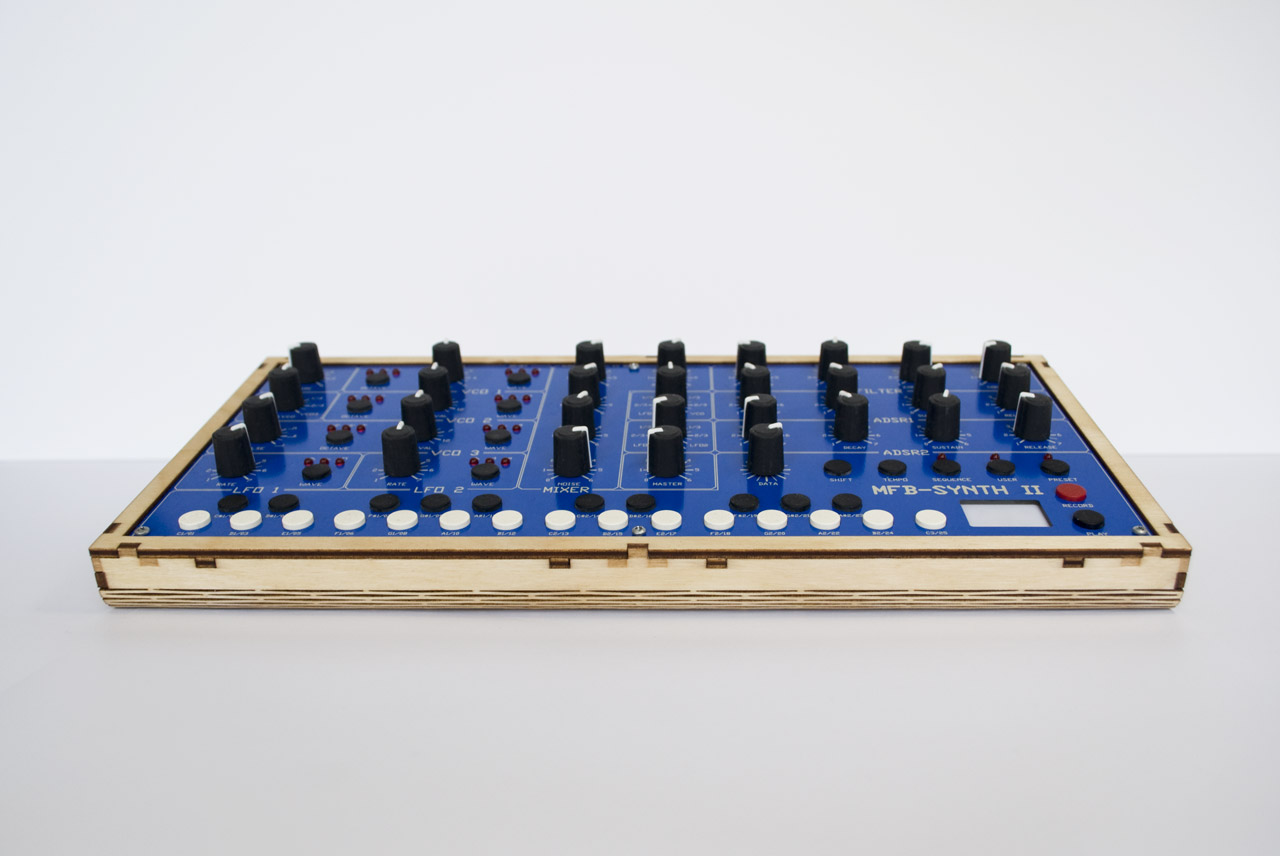
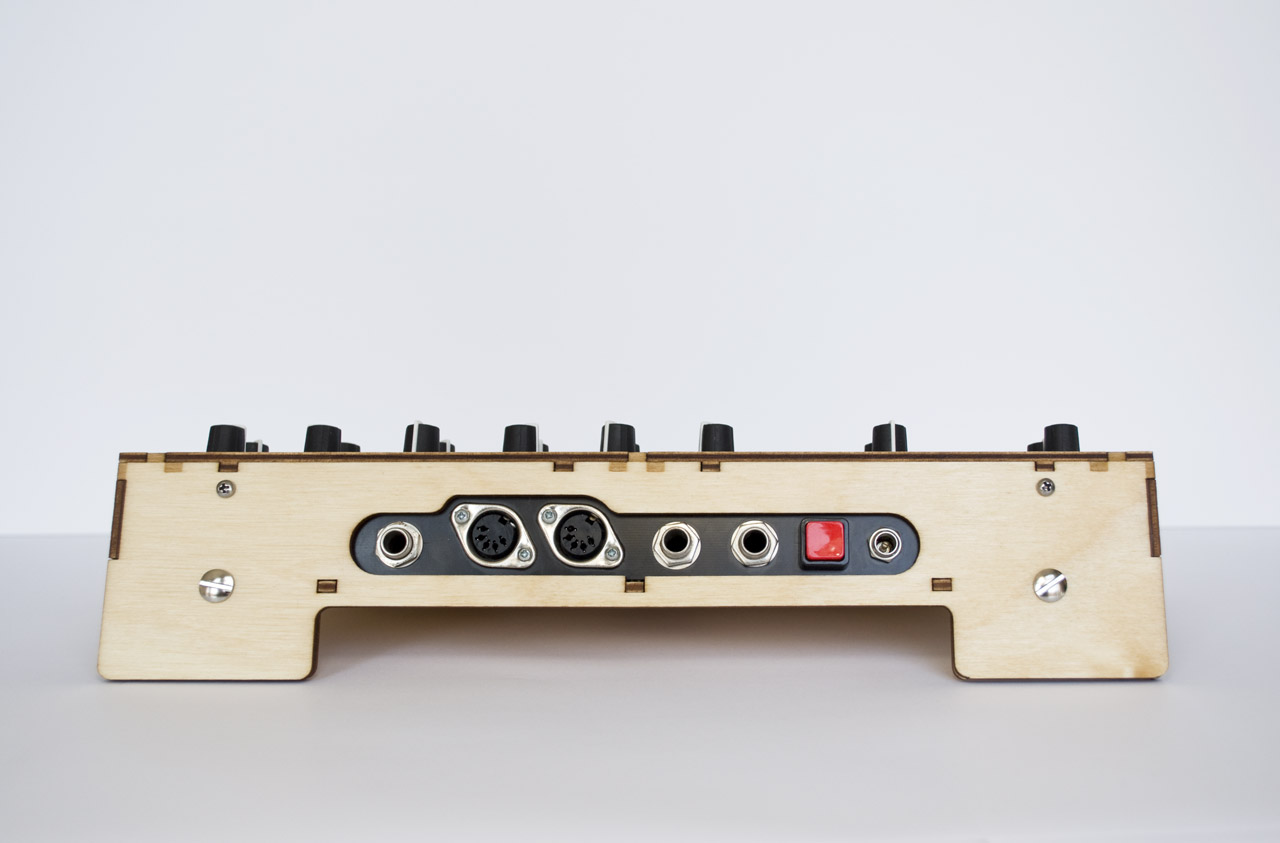
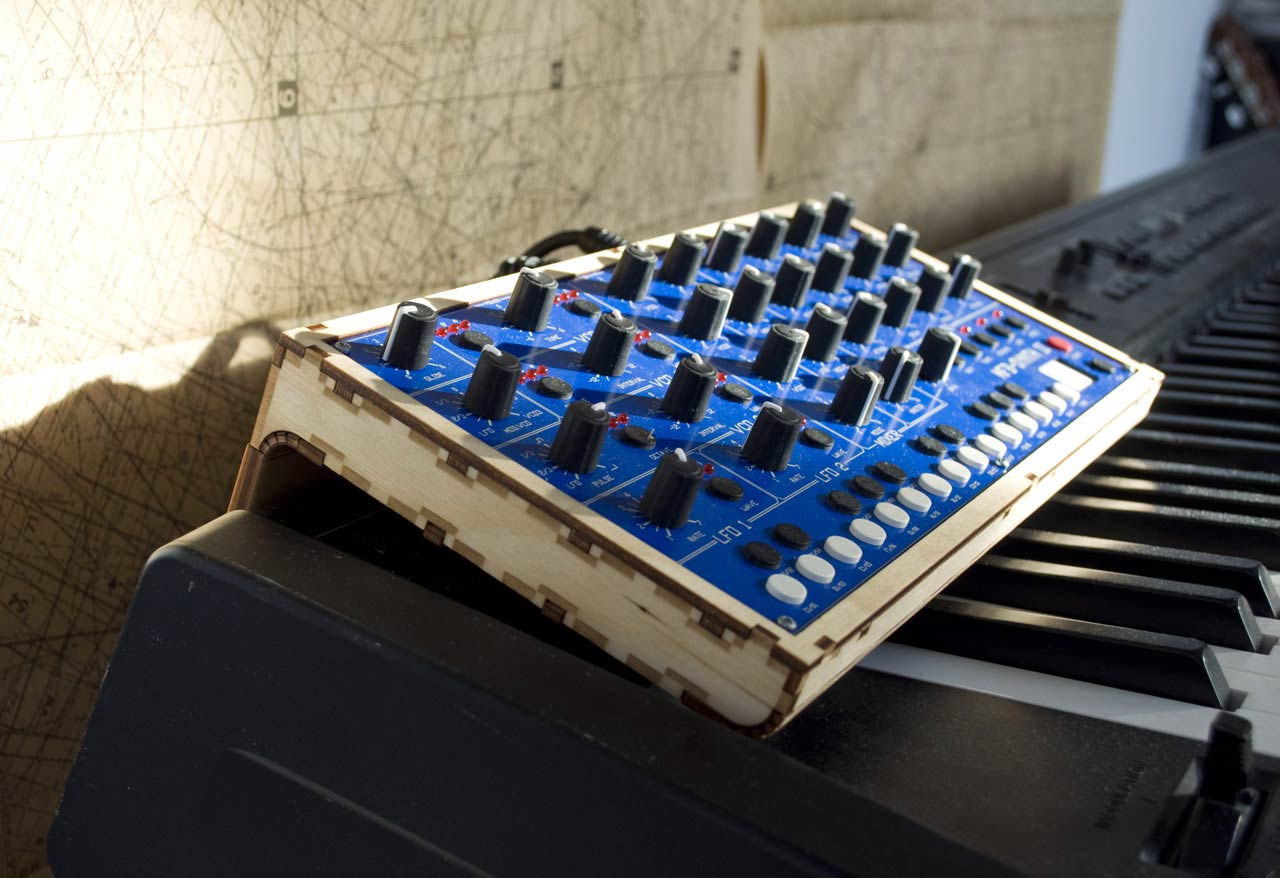
Background
But why?!..

Musicians like guitarists or violin players feel strongly connected to their instrument and care for it in a much more devoted way than with any other object; they often even give it a name. This could be caused by several factors: the used material and finishing, the attention to detail put in the instrument, the personalised look/uniqueness of the instrument, the damage/patina due to experience using it, among many other reasons. The attraction to the instrument is also strengthened because it often needs maintenance on the material, components or finishing, like polishing, oiling, adjusting strings, etcetera.
With many non-acoustical and electronic instruments this usually isn’t necessary and for many of these instruments it results in a rather lifeless appearance. It could also be because these electronic instruments are being produced in a highly automated production line and therefor are not only less unique, but often any potential irregularity in the materials has been ‘designed away’ in order to optimize the reliability and minimize the costs.
With many non-acoustical and electronic instruments this usually isn’t necessary and for many of these instruments it results in a rather lifeless appearance. It could also be because these electronic instruments are being produced in a highly automated production line and therefor are not only less unique, but often any potential irregularity in the materials has been ‘designed away’ in order to optimize the reliability and minimize the costs.
In this project I have looked into the possibilities to use an automated production technique with a characterful material and see if this can lead to a product that is more likely to be bonded with, because of its unique character and also because of its need for material care. At the same time I have tried to find a balance between a characterful enclosure and an enclosure that is designed for an automated production process.
The modified instrument, the MFB Synth II, is an electronic monophonic synthesizer: an analog module with controllers that allows the musician to modify an electronic signal generated by voltage controlled oscillators. The instrument modifies the electronic signal based on the settings made by the player. Finally the electronic signal exiting the device is amplified and fed to a speaker.
Since it is not an acoustic instrument the housing of the instrument can have any form and can be made out of any material without influencing the sound.
The modified instrument, the MFB Synth II, is an electronic monophonic synthesizer: an analog module with controllers that allows the musician to modify an electronic signal generated by voltage controlled oscillators. The instrument modifies the electronic signal based on the settings made by the player. Finally the electronic signal exiting the device is amplified and fed to a speaker.
Since it is not an acoustic instrument the housing of the instrument can have any form and can be made out of any material without influencing the sound.